Today's manufacturing plants are transforming operations by leveraging the interconnectedness of thermal processes with ammonia heat pumps. Once deemed a byproduct, waste heat now powers diverse facility needs, driving efficiency, sustainability, and competitiveness.
In today's rapidly evolving industrial landscape, manufacturing plants face increasing pressure to maximize operational efficiency and minimize costs while simultaneously meeting their current and future environmental goals and objectives. Achieving energy efficiency and reducing greenhouse gas emissions are no longer optional but rather essential components of sustainable and competitive business practices.
In this context, the utilization of sustainable technologies such as ammonia heat pumps is emerging as a promising solution for manufacturing facilities that rely on refrigeration processes. The new mindset is to look at the total thermal solution and to create, capture, and reuse thermal energy within all systems. That is where the addition of ammonia heat pumps presents a measurable and meaningful investment to help your plant's sustainability from both a business and environmental perspective.
A Holistic Approach to Thermal Management
Industries are increasingly recognizing the relationship between their operations and the environmental impact. Manufacturing processes particularly generate significant thermal energy, typically wasted into the atmosphere because this low-temperature heat remains largely unusable within the plants, contributing to wasted potential and missed opportunities for energy efficiency. However, industrial heat pumps can upgrade this low-grade heat to higher temperatures that can then be utilized for various purposes within facilities. This not only optimizes energy usage but also reduces emissions from burning natural gas for boiler heating.
By integrating ammonia heat pumps into refrigeration processes, manufacturing plants use the energy that has already been paid for. By doing so these facilities are posed to achieve substantial reductions in energy consumption and greenhouse gas emissions and stay aligned with corporate sustainability goals and regulatory requirements.
Natural Gas Dilemma: Escalating Costs and Tightening Regulations
As natural gas prices steadily increase alongside the imposition of carbon taxes, industrial heating needs to confront a pressing predicament. While traditional natural gas boilers can provide reliability and affordability, they pose wide environmental concerns due to their resulting carbon emissions and lower energy efficiency (usually operating at efficiencies below 90%). Consequently, these boilers consume more energy and incur higher operational costs. With governments enforcing higher carbon taxes to incentivize emissions reductions, the operating costs of natural gas boilers are anticipated to rise significantly, further straining industrial budgets and profitability. Additionally, natural gas deposits globally are running out, increasing the insecurity about their long-term availability.
The Green Promise of Ammonia Heat Pumps
From a business perspective, investing in ammonia heat pumps offers tangible benefits beyond immediate cost savings. Ammonia, used as a refrigerant, boasts zero Global Warming Potential (GWP) and zero Ozone Depleting Potential (ODP). Its thermodynamic properties allow for high performance, with Coefficients of Performance (COPs) generally exceeding 3.
Industrial heat pumps position manufacturing plants as leaders in sustainable practices, enhancing their reputation and market competitiveness. Moreover, as environmental regulations continue to evolve and carbon pricing mechanisms become more prevalent, the adoption of environmentally friendly technologies becomes imperative for long-term viability.
In summary, the incorporation of ammonia heat pumps
into manufacturing processes represents a strategic opportunity for companies
to achieve their operational, environmental, and financial objectives
simultaneously. By embracing a holistic approach to thermal management and investing
in sustainable solutions, manufacturing plants can pave the way for a greener,
more efficient future while maintaining a competitive edge in the market.
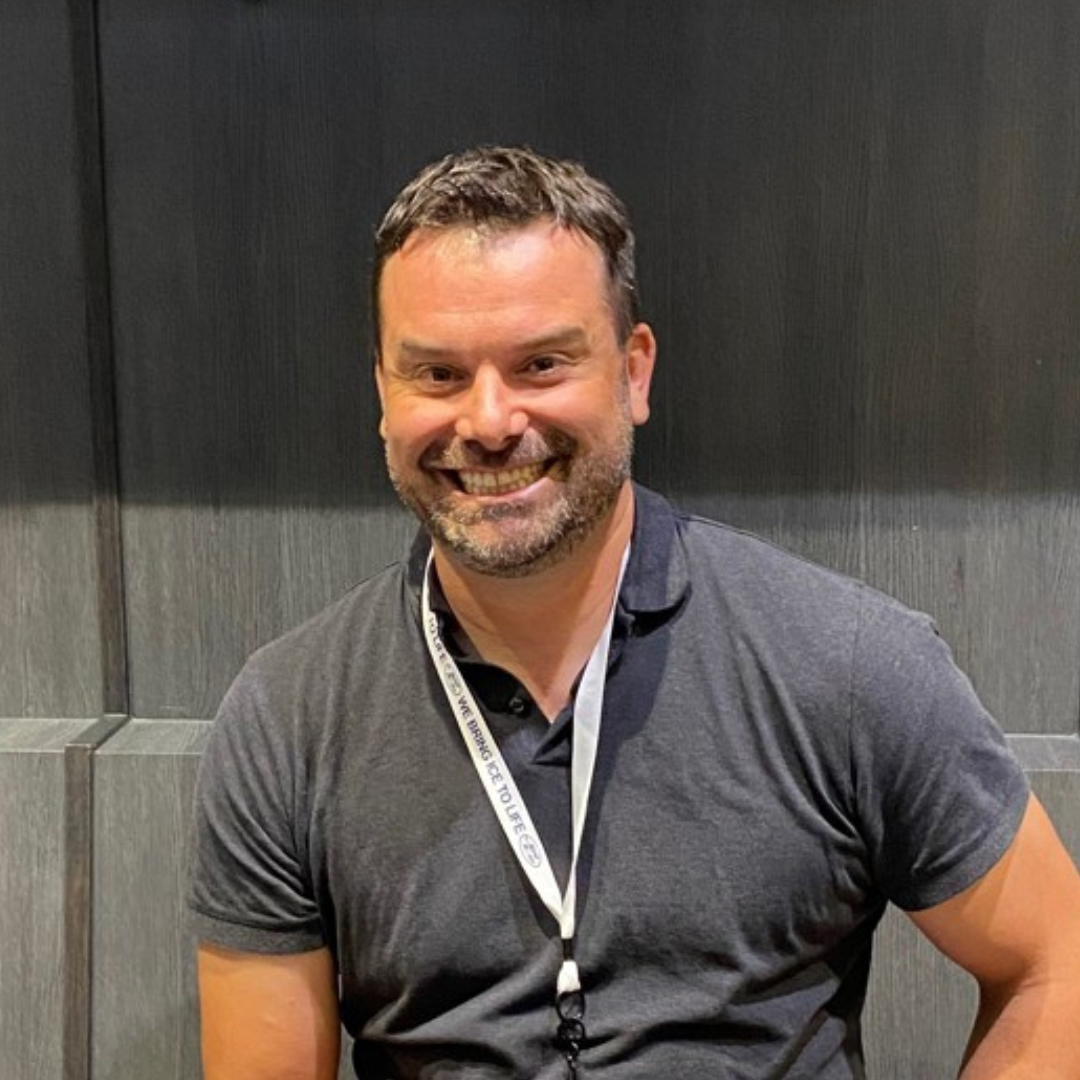
DAVID FAUSER - DIRECTOR OF SALES
David has been with the CIMCO for more than 20 years. During that time, he has been involved in hundreds of new plant designs and retrofits throughout North America. David has a passion for ice sports and sustainability, and was instrumental in CIMCO’s decision to drop recreational ice rink packages that use refrigerants with high global warming potential from its lineup, because of their climate impact. He is a strong voice on environmental issues and legislation, and is a thought leader in the industry. He believes that there is a solid business case to incorporating net-zero and net-zero-over-time strategies to today’s industries.
e: dfauser@toromont.com
Related Posts
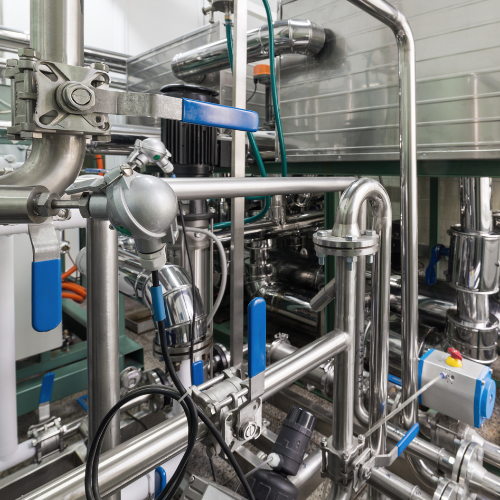
Comparison of Key Refrigeration System Components: Making the Right Choice for Your Operation

Decarbonization Trends Shaping Industries
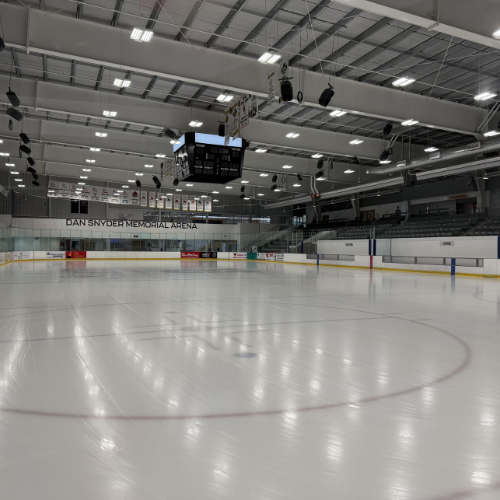
Woolwich Memorial Centre Achieves Energy Excellence with CIMCO’s Eco Chill
|