Have you considered the benefits of upgrading to net zero? Here are some quick tips for increasing efficiency and reducing the overall operating costs of an existing refrigeration system.
HVAC&R systems have a key role to play in curbing emissions and addressing the climate crisis. Lowering both direct emissions (from the refrigerant) and indirect emissions (from the electricity) is key for not only saving the planet but saving money too.
However, installing a brand-new, state-of-the-art refrigeration system is not always feasible. This doesn’t mean you can’t improve how your existing system performs. What are some potential modifications you can make today to upgrade your plant?
Refrigerants
It is common for large refrigeration installations to be charged with natural refrigerants like CO2 (R744) or ammonia (R717) as their main refrigerant. This is because natural refrigerants are extremely efficient and do not impact the environment if released into the atmosphere, making them the most sustainable, future-proof option. They are also readily available at a low cost.
Unfortunately, when it comes to HVAC equipment, natural refrigerants are not as prevalent as they are in refrigeration. Instead, most HVAC systems use some form of synthetic refrigerant, called fluorinated gas (f-gas). These f-gases are considered harmful to the environment because of their high global warming potential (GWP) and can often be more inefficient than natural refrigerant alternatives. The opportunity lies in merging these HVAC refrigeration loads with that of the main refrigeration system. This results in fantastic energy savings because you’re reducing the major equipment needed to accomplish the same amount of cooling.
Switching all your HVAC&R systems to natural refrigerants offers the added benefit of reducing costly leaks as f-gas systems tend to leak at a significantly higher rate. Not only that, but the price of these high-GWP synthetic refrigerants will continue rising in the face of stricter regulations and phasedowns. This is impacting availability too; do not expect f-gases to be readily (or cheaply) available in the future. All the more reason to switch equipment to natural refrigerants wherever possible.
Energy Monitoring
Management 101 says “if it is not measured, it is not managed.” A simple upgrade to your existing automation control system to also include power metering for all the equipment panels may do just the trick here. Power metering provides trending and easily readable heat map data. This can be updated at whichever frequency you require (hour by hour, minute by minute, day by day, etc).
Power metering enables a quick view of how the system is operating, also highlighting spikes in energy usage. This allows the user to dig deeper into high energy-points to potentially uncover inefficiencies. This also allows you to finetune equipment set points and immediately see its impact on energy use, rather than having to wait for the monthly utility bill.
Reducing System "Lift"
"Lift" in a refrigeration system refers to the difference between the suction and discharge pressures of the compressors. Reducing lift will improve compressor efficiency by either a) increasing the suction pressures or b) reducing discharge pressures. Generally, increasing suction pressure increases compressor capacity, while decreasing discharge pressure should decrease compressor brake horsepower.
As a rule of thumb, the efficiency of a compressor operating in an ammonia refrigeration system increases by about 2% per degree Fahrenheit increase in suction temperature. If it is possible to adjust the operating temperatures within the facility (most likely in the dock and cooler areas), then there is potential for energy savings.
VFD Motor Starters
In modern system design, variable frequency drives (VFDs) are usually fitted to the evaporators, evaporative condenser fans, and one screw compressor per operating temperature. Typically, this is the simplest method for reducing the energy consumption of a refrigeration plant.
Adding VFDs is extremely beneficial for reducing the defrost frequency of a system. It allows for closer monitoring of the defrost requirements of each evaporator and can create energy savings by extending the time between, as well as the length of, defrost cycles. For reference, a typical defrost can cost somewhere around $0.15 to $0.20 per cycle . This quickly adds up.
Compressor Oil Cooling
In most refrigeration systems that I see, screw compressors are equipped with thermosyphon oil coolers, which are quite efficient. Why not rather consider glycol oil cooling? This option can contribute to heat recovery gains if the facility uses the warm glycol after it’s been used to cool the compressor oil. This won’t reduce the refrigeration system’s operating costs but may help to reduce some auxiliary operational costs.
Heat Recovery
Heat recovery can be used for a variety of functions within a facility. Typically, large facilities will pre-heat incoming city water as much as possible using "free" heat from the refrigeration system before it goes through a power-hungry boiler to reach the 140°F+ (60°C) required for sanitation/wash-down. This will also reduce the amount of heat that needs to be rejected by the evaporative condensers, saving some of the energy required to operate the fans and water pumps.
Ammonia Anhydrator
Although auto-purgers are commonly used on the high-temperature side of refrigeration systems to eliminate non-condensable gases, these leave behind all the moisture and condensable impurities. An anhydrator is designed to eliminate these efficiency-robbing substances on the low-temperature side of your system. They can be installed on both low-temp and high-temp systems. Although anhydrators are more commonly found on the low-temp side (since they operate in a vacuum and have a greater likelihood of pulling in impurities) they can be beneficial to high-temp systems too.
Start Somewhere
There are always many options to consider when upgrading a refrigeration plant. The list shared above offers some suggestions but is by no means exhaustive. Often plant operators themselves have additional suggestions specific to the way they operate, highlighting additional low-hanging fruit.
CIMCO is passionate about helping facilities reduce their refrigeration carbon footprint and we welcome further discussion on the subject. What have you done to improve your plant's operation?
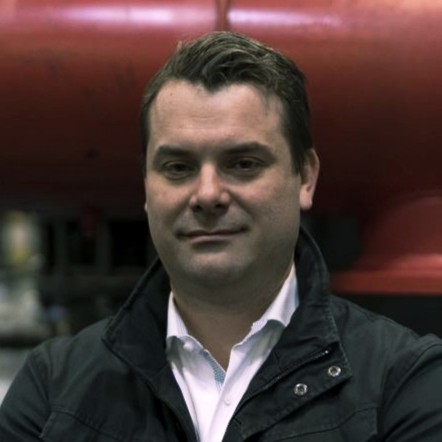
DAVID FAUSER - DIRECTOR OF SALES
David has been with the company for more than 20 years. During that time, he has been involved in hundreds of local and professional new rink designs and retrofits throughout North America. David has a passion for ice sports and sustainability, and was instrumental in CIMCO’s decision to drop recreational ice rink packages that use refrigerants with high global warming potential from its lineup, because of their climate impact. He is a strong voice on environmental issues and legislation, and is a thought leader in the industry. He believes that there is a solid business case to incorporating net-zero and net-zero-over-time strategies to today’s ice rinks.
Related Posts

Decarbonization Trends Shaping Industries
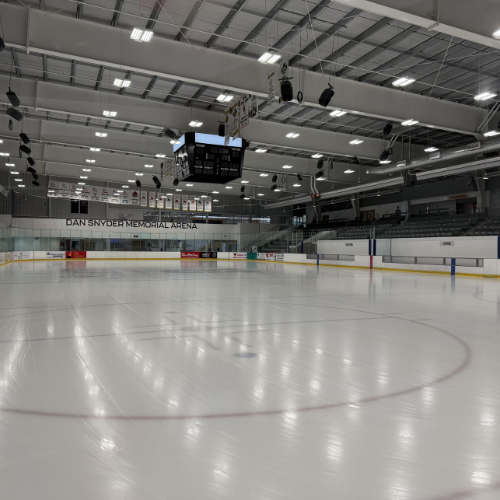
Woolwich Memorial Centre Achieves Energy Excellence with CIMCO’s Eco Chill
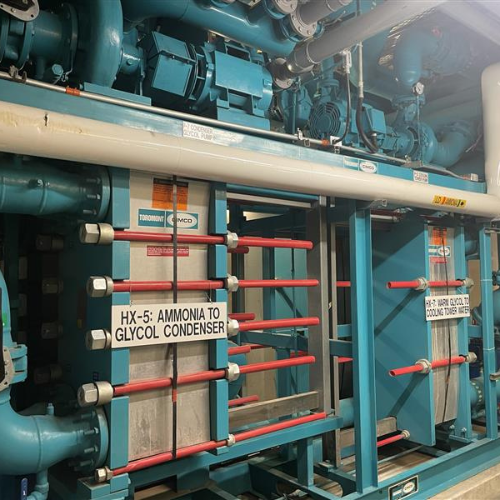
10 Simple Fixes to Boost Efficiency in Aging Refrigeration Plants
|