10 years after installation, CIMCO's ECO CHILL® Ammonia Heat Pump has and continues to support the demand and requirements of the Maple Leaf Food plant allowing the processing of 18,000 hogs per day, 5 days a week, on a yearly basis, and usage upwards of 500 usgpm of 140ºF water for up to 22 hours a day.
Overview
Being one of the largest providers of products in the sustainable food industry, there is a need for refrigeration machinery, and that is where CIMCO came in with the installation of their ECO CHILL® Heat Pump. CIMCO’s ECO CHILL® Heat Pump has been using refrigeration waste heat, generated by the refrigeration process, for a number of years by collecting, recycling and re-using this heat for building and product heating. The function of an ammonia heat pump, using a conventional compressor’s discharge heat as the energy source, provides a higher level and quality of heat. This is particularly true where the use of refrigeration and hot water are both in high demand. CIMCO took this concept to Maple Leaf Foods, and in a joint effort the design, construction and implementation of a 1,000 HP CIMCO Ammonia Heat Pump went from a vision to a reality, leading to Maple Leaf Foods reaping the benefits for nearly 10 years now.
In this plant, refrigeration requirements have been served by a CIMCO multi-temperature 14,000 HP ammonia refrigeration system generating more than 8,600 TR for years. The hot water requirements are mandated by the Maple Leaf Foods “Hazard Analysis and Critical Control Point” (HACCP) program and can surpass 500 gallons per minute, which traditionally relied on NG boilers and direct contact water heaters.
The plant’s HACCP program mandated that the hot water be available at no less than 132ºF. With the ECO CHILL® Ammonia Heat Pump, the plant discharge ammonia gas at 140 to 160 psi is used as suction gas in the heat pump compressor, boosting it to more than 185ºF on the condensing side, and enabling the system to achieve the required water temperature.
Product Outlook and Targets
Our design and development targets:
- Generating 140ºF water output capability.
- Making it easily adaptable to existing facilities and users.
- Utilizing readily available equipment that could operate at the pressures that would be encountered in the 400 – 450 psi range and higher.
- Maximizing heat transfer and system efficiencies by using such technologies as plate heat exchangers, high thermal conductivity heat transfer mediums and advanced automation strategies.
- Being economically viable in hot water flow rates of 75 to 700 usgpm hot water output.
General Information
- Owner: Maple Leaf Foods
- Project Type: Pork processing
- Operation (per year): 12 months/5 days per week/22 hours per day
Heat Pump System
- Hot water heating
- Frick 1000 HP screw compressor, liquid injection
- Alpha Laval dual plate and frame condensing
- Operating pressure: 150psi/420psi
Electrical Input
- Compressor Power Net: *150 HP
- Motor Efficiency: 95%
- Energy Rate: $0.05/KWH
- Electrical Costs: $39,800 annually
Run Time
- Daily: 18 hours
- Weekly: 5 days
- Annual: 52 weeks
- Runtime: 4680 hours
Heat Recovery Integration
- Hot gas heat for make-up air
- Water preheated
Thermal Storage
- Modulates variations in flow rate to avoid starting/stopping
- Approx. 15,000 gallons
Refrigeration System Information
- Compressors: Frick
- Horsepower: 14,000
- Plant Style: Pumped liquid/evap. condenser
- Total System Tonnage: 8600 TR
- Refrigerant: R-717
- Evaporator Style: Pumped liquid, hot gas defrost
Integrated Controls System Design
- CIMCO Industrial Automation
- Indicates temp/out
- Volume/flow rate
- Controls condensing and run pressures
- Controls water flow rate and bypass
- Controls compression in conjunction with plant refrigeration system
Natural Gas Savings
- Fluid: Water
- Flow rate: 150 usgpm
- Inlet: 85ºF
- Outlet: 140ºF
- NG Boiler Eff: 80%
- Gas Cost: $0.30/cubic Meter
- Annual Saving: $223,599.00
Related Posts
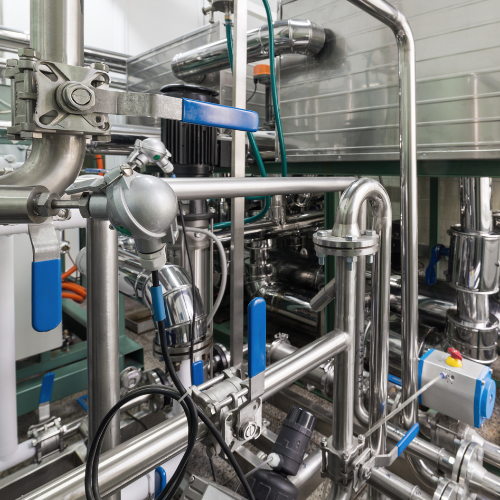
Comparison of Key Refrigeration System Components: Making the Right Choice for Your Operation
.png?sfvrsn=26cbdc22_3)
Ammonia Heat Pumps Achieve 185°F, Ditch the Boiler for Food & Beverage Production
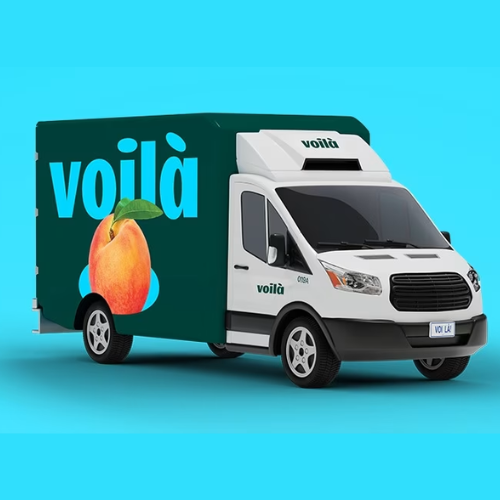
CIMCO Delivers Sustainable CO₂ Cooling for Sobeys' Automated Facility
|